How does it work?
AmiTrace allows you to plan the traceability process and implement mechanisms to maintain production quality at a satisfactory level. In addition, the software can support the execution of production orders. In the absence of automatic solutions in key production processes (e.g. manual operations, obsolete machines) the system allows configuration and implementation of standard production forms providing the required data to the system. AmiTrace is fully compatible with the AmiProces system (amiOrder + amiTrace + amiOEE). It can be one of its modules or operate independently as a separate system. AmiTrace is used in various industry sectors based on retail production, such as automotive, household appliances or some heavy industry branches.
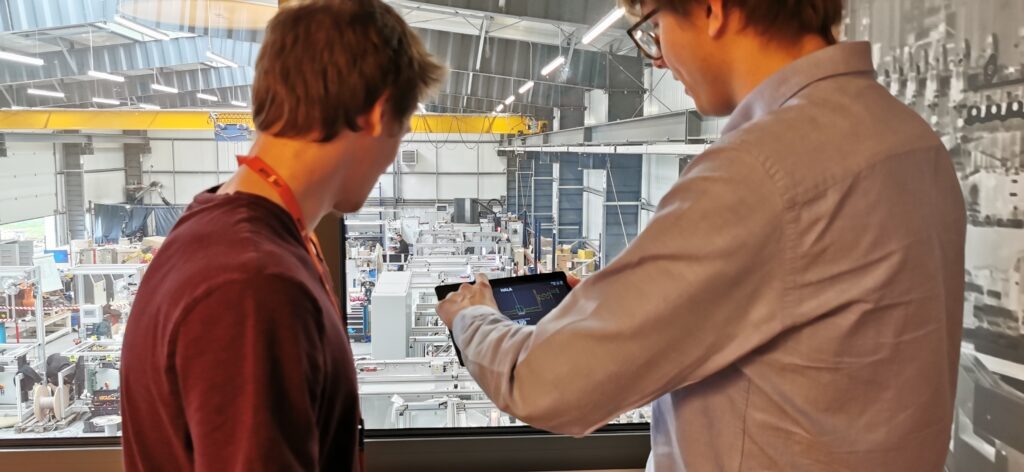
What is traceability?
It is (identifiability) traceability, the ability to identify a product and verify its path based on various sources of information. In industry, this means the greatest possible transparency and traceability of the manufactured product. In practice, it is about the acquisition of all production data, which allows for product identification in a specific time perspective, in terms of quality, and tracking its genealogy (also in historical terms).
System components
The MES module enables:
- defining specific production areas,
- assignment to the area: (determination of the type and preceding units, determination of the method of data delivery, definition of the type and source of parameters),
- defining and configuring production units,
- defining parameters and their measurement units: (assignment to production areas, allocation to production units),
- defining production variants,
- defining and categorising technical drawings,
- system operation diagnostics.
The communication module allows you to:
- define communication channels,
- define PLC controllers,
- assign an IP address, rack number and/or slot number,
- connect diagnostics.
The reporting module is primarily:
- analysis of the effects of the full traceability process of production,
- the ability to enter comments at key stages of reporting,
- the ability to configure subscriptions to selected reports to any network location.
